Material handling applications present some of the most challenging equipment customization scenarios. Changes to process or upgrades to increase safety or efficiency, combined with the limitation of existing equipment integration, all pose many difficulties. This is the scenario that brought this customer to us at Avon Lake Sheet Metal.
In this project, a Cleveland manufacturer needed a custom fabricated powder batch weigh system fabricated. Their current configuration was creating a serious ergonomic issue, which needed to be addressed to maintain maximum employee safety. What we provided this customer was a complete turnkey solution that not only met their safety concerns, but price point and scheduling as well.
The process began with the development of a design that would provide all the features required, and integrate seamlessly with the existing material handling system. The final design included a stainless steel product and weigh hopper with aluminum lids, dust covers and galvanized steel dust collection duct work, carbon steel structural supports, as well as access stairs and a walkway. Additionally, we also provided a roller conveyor system, vibratory feeders, load cells, and PLC controlled weighing system.
The development of the structural and mechanical design elements was 3D modeled prior to fabrication. The fabrication process used a wide range of our fabrication capabilities and included sawing, shearing, forming, rolling, laser cutting, and welding. All of the material contacts points were composed of stainless steel that was polished to a mirror finish; all of the structural steel elements were painted. The finished unit was composed of material that varied in thickness from 16 gage up to 0.50”. The finished dimensions measured 20’-4” in length and 18’-9” in width. Once completed, we also provided installation on-site, with minimal disruption to operations.
To learn how a single source equipment fabrication solution can help your operational efficiency, contact us directly.
Capabilities Applied/Processes | Primary: Product Designing • Coordinated Structural and Mechanical Design • 3D Modeling Fabricating • Laser Cutting • Sawing • Shearing • Rolling • Forming • Welding Secondary: Polishing Painting Field Installation Integration of 3rd Party Vibratory Feeders, Load Cells, and PLC Weighing System. |
Overall Part Dimensions | Length: 20’-4” Width: 18’-9” Material Thickness: 16 Ga. to 0.50” |
Tightest Tolerances | ±0.062 in. |
Material Used | Type 304 Stainless Steel Hoppers, Carbon Structural Steel, Galvanized Steel Ductwork, Aluminum Hopper Lids |
Material Finish | Painted Carbon Steel, Bright Finish Stainless Steel |
In Process Testing / Inspection Performed | Dimensional Inspection, Functionality Testing |
Delivery Location | Cleveland, OH |
Standards Met | Customer Specifications |
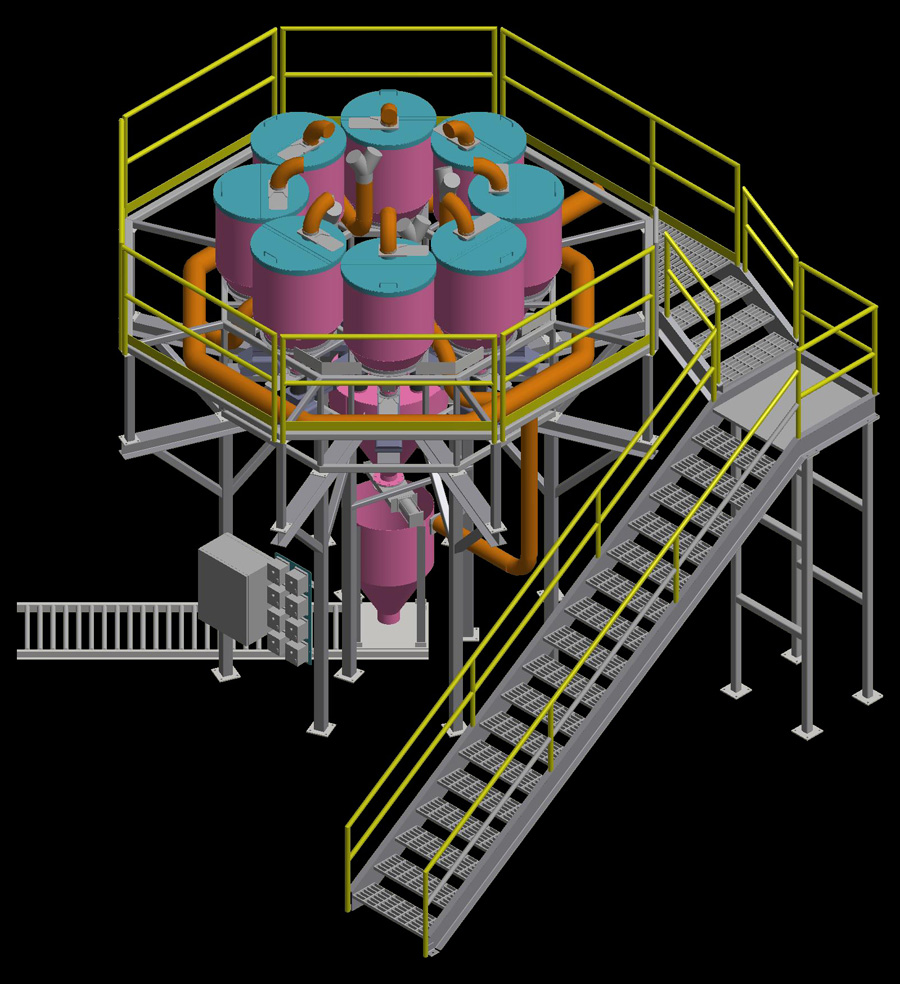
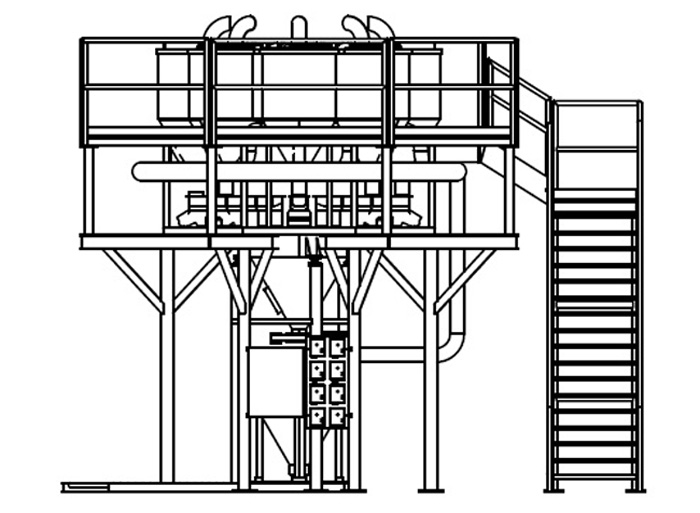
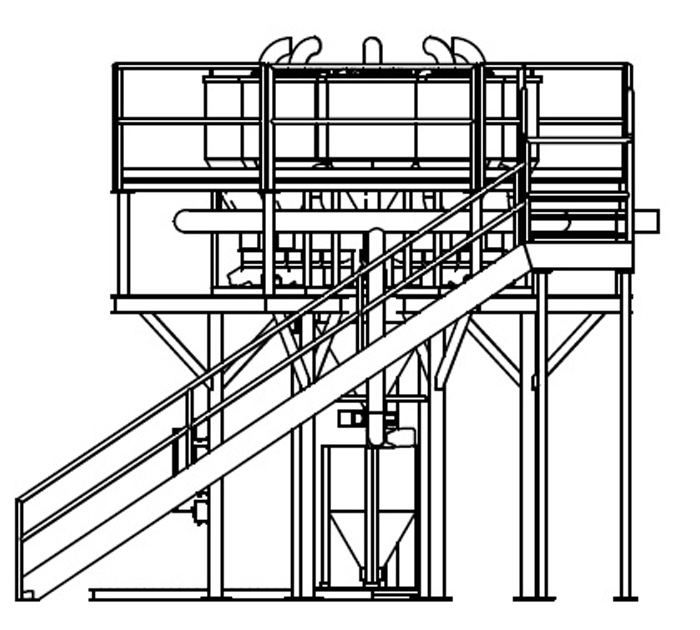
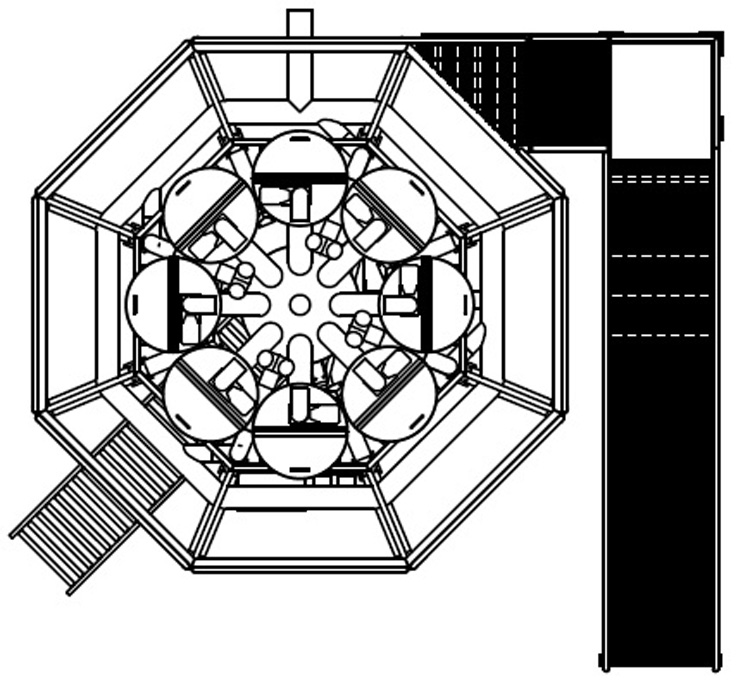